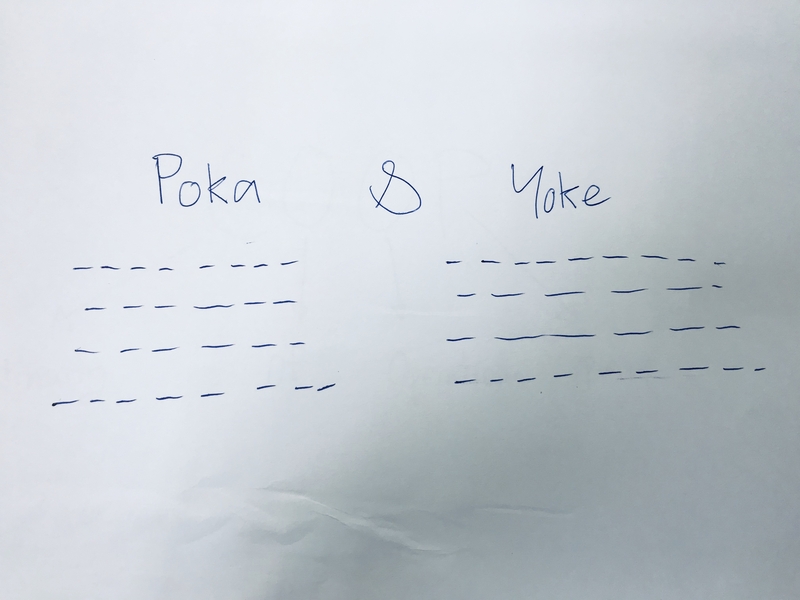
We have many process analysis tools in Lean, but the poka-yoke is one of the most popular ones. In any given process with human operators, mistakes and errors are bound to happen. These lead to defects, which are part of the eight wastes of lean. Poka-yoke, also known as mistake- and error-proofing, helps eliminate mistakes entirely.
We will discuss what poka-yoka – pronounced as poh-kah yoh-keh – is, its history, the benefits and some examples. This should briefly introduce you to the concept and why it is useful. While it is mostly used in the manufacturing and service industry, its application is universal.
What is Poka-Yoke?
Poka-yoke is an automatic mechanism, whether it is a device or method, that prevents anyone from making a mistake or error. But if the mistake or error can’t be prevented, a poka-yoke will make it obvious that it has occurred. That way, the source can be identified and eliminated.
A Brief History of Poka-Yoke
The person who coined poka-yoke is Shigeo Shingo in 1960. He was a Japanese industrial engineer who worked for Toyota. Shingo was one of the top experts on manufacturing practices at the time. And apart from the poka-yoke, he is mostly known for standardizing the Toyota Production System (TPS), which is a popular manufacturing methodology for eliminating waste and increasing efficiency.
The term poka-yoke itself literally means “mistake-proofing.” Interestingly enough, it was originally called baka-yoke or “fool proofing.” But it was later changed, considering it had negative connotations and the Japanese have a culture that highly favors politeness.
The Benefits of Poka-Yoke
One of the biggest benefits of poka-yoke is that it minimizes the chance of human error in a process. It ensures that all conditions are right before the next step in the process occurs. The end result is that the process will produce little to no defects.
Other than that, poka-yoke also comes with the following other benefits:
- Increase in quality: With the poka-yoke making sure that the process doesn’t produce defects, the quality goes up. This means stakeholder and customer satisfaction goes up as confidence levels in your process consistently producing quality products increases.
- Reduction in costs: The biggest problem with defective products is that they increase the amount of waste. And since they need to be replaced, the costs of production rises as the number of defects rise as well. Fewer defects mean fewer costs.
- No high-skill requirement: if a process has a bigger margin for error, it needs operators to be highly skilled to operate it. If the operator doesn’t have the skill, the organization has to spend resources to either train them or hire a more skilled worker. With a poka-yoke automatically preventing mistakes and errors, the skill requirement goes down significantly.
- Increases safety: Safety is a major concern in the workplace, especially when workers handle hazardous materials. With poka-yoke eliminating human error, safety in the workplace goes up by a great margin.
- Reduces the need for quality checks: With an error-eliminating device or method embedded into the process, there’s no need for extensive quality checks. The poka-yoke will detect or predict any problems without relying too much on inspectors.
- Speeds up the process: With less manual inspections needed, work progresses at a faster rate without sacrificing quality. Moreover, the workers focus on what they do best, which makes the work less boring and repetitive.
Example of a Poka-Yoke
You don’t need to go far to see an example of a poka-yoke – they are around us all the time. One example is charging your phone with a USB. When you try to plug it in the wrong way, the USB does not enter. It only enters when you flip it and plug it in the right way.
Another famous example is the automatic car. Manual cars allow you to start your car while in gear, but in doing so the car will move and accidents can happen. An automatic car, however, will not start unless it is in neutral or park – hence eliminating the error.
Conclusion
With poka-yoke, mistake-proofing is built into the process, significantly reducing or eliminating human error. While we’d all like things to go smoothly all the time, when humans are involved things can go wrong. This is why the poka-yoke has become one of the most popular process analysis tools in Lean.
It’s important for companies to have poka-yoke in their systems design. Mistake proofing and trying to eliminate error is important to the safety and quality of the company and their products – as well as the workers. All companies should have some form of “mistake-proofing” or putting in certain systems that can help cut down on mistakes.