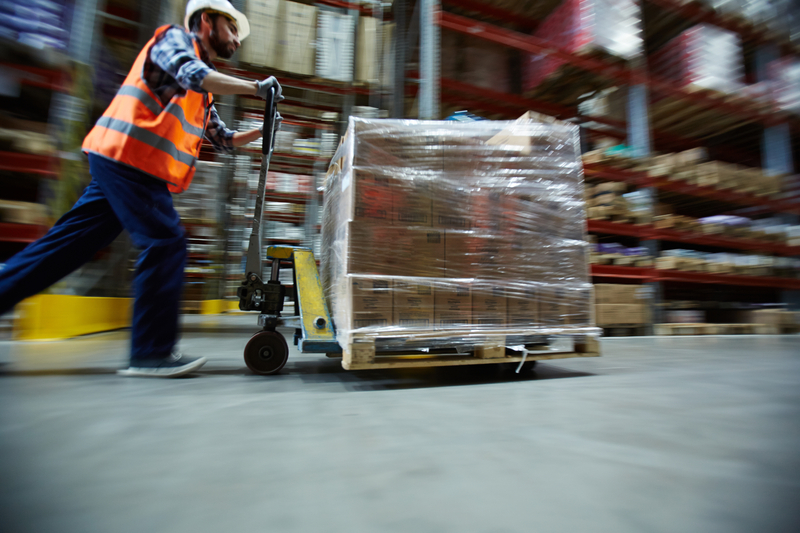
Warehousing is the storage of goods intended for sale or distribution in a warehouse. However, it becomes more complex when this process comes face-to-face with the dynamic nature of business operations. These require a high level of efficiency to minimize costs and maximize profits.
Luckily, Six Sigma, with its set of management techniques, can be used to improve the warehousing process. If done correctly, applying Six Sigma’s data-driven and statistical tools and techniques to warehousing provides organizations with a way to eliminate issues permanently. Furthermore, it helps them discover performance measures that highlight areas of further improvement.
The goal of Six Sigma is to reduce the number of defects to 3.4 for every million opportunities. This is regarded as a sigma level of 6, which is the highest and most sustainable level of optimization. This increases the levels of customer satisfaction, as well as increases the organization’s bottom line.
Here are ways in which Six Sigma can benefit a warehousing operation.
Customer Loyalty
Customers not only notice but appreciate it when an organization has taken the time to improve efficiency and quality. In the end, customers become loyal since they have confidence in the organization’s ability to deliver high-quality and affordable products with little-to-no hassles.
Six Sigma provides an organization with the tools they need to convert customers into loyalists. When customers see that the warehouse is shipping products with speed and accuracy, they will be satisfied, especially if that is a pattern rather than a fluke. But if errors aren’t caught in the warehousing process and customers start receiving products with defects, they will quickly lose confidence in the organization’s ability to deliver. This will make them hesitant to place additional orders because it might feel like they’re gambling on quality.
All errors need to be identified and corrected right – the hallmark of a Six Sigma organization. Six Sigma empowers the warehousing team with a comprehensive strategy for handling errors by eliminating them at the root so they never happen again. That way, the warehouse operation can focus on satisfying customers instead of resolving their complaints.
Transforms Organizational Culture
Six Sigma is about improving the entire culture of the organization. Everyone in the organization, from sales and finance to manufacturing and warehousing, knows what they need to make the organization more efficient.
With clearly defined roles and milestones, it becomes easier to rally people behind the common goal. So not only will the warehouse team be able to work towards making their operation more efficient, but they will work with others to ensure the entire organization is efficient as well.
Reduces Costs
Satisfying customers is one of the major objectives of the warehousing team. And what better way is there to achieve this than to reach a sigma level of 6. By streamlining the warehousing process, on top of reducing or eliminating defects, the team can effectively reduce costs and transfer the savings to the customer.
Furthermore, keeping costs down also means that the organization can increase its bottom line. This means that shareholders will also be pleased and more willing to pour more resources into the warehousing process to make it more efficient.
Improves Quality
Naturally, when the warehouse manages to get rid of errors, quality will go up. Six Sigma provides teams with the necessary statistical tools to gather warehousing data. By analyzing the data, they can extract insights that can help them ensure that customers don’t get poor-quality products.
The data that the warehouse team gathered can also be shared with other departments in the organization. This will help other teams throughout the organization improve their processes as well so they too can produce quality output and cut costs.
Conclusion
The Six Sigma methodology is a great tool for improving the warehousing process. In turn, this increases customer loyalty, reduces costs, and improves quality. Furthermore, since Six Sigma happens on the organizational level, everyone works together to make everything efficient.
No responses / comments so far.