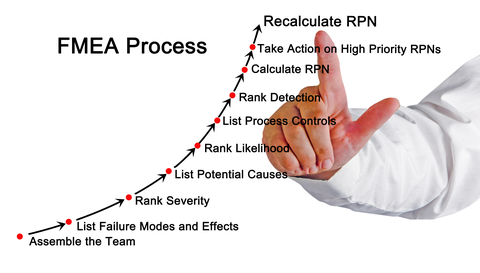
Breaking Down the FMEA (Failure Mode and Effects Analysis) Process
Failure mode and effects analysis or FMEA is a well-known technique for analyzing failures in any operation in a systematic manner. It can be very effective when applied correctly, and has a long-running history of successful usage in many industries. When reliability is a top concern in your current operations, you should definitely look into implementing FMEA if it matches the profile of your business.
Basic ideas
A great thing about FMEA is that it can be applied on multiple levels including abstract ones in order to best suit the current state of your process design. This means that you can effectively use FMEA to study the core functionality of each component in your production, and after that carry over the analysis to the actual hardware parts that implement this functionality. This can have powerful implications when you want to study the core design of your product itself, rather than its final stages.
When applied correctly, FMEA can lead you to a design that works on every level, and produces adequate results that are within reasonable bounds. What’s more, it can help you continuously pick from different designs as you keep improving your business over time, in order to maintain it in a state where failures are kept down to a minimum. On the other hand, you will also ensure that safety stays at sufficiently high levels.
Important assumptions
There are some assumptions that have to be made when applying FMEA, and if those prerequisites are not met, you may get incorrect results from your analysis. For example, you should not study the possibility of multiple failure modes existing at the same time. While that’s a valid assumption in some contexts, it can negatively impact the way you analyze the results of FMEA, and you should therefore align your thoughts in a different direction.
It’s also important to ensure that all basic prerequisites for successful operation are met in the first place. This means that the process is supplied with all its necessary resources, and it’s powered adequately. Otherwise you’re not going to be able to count on the validity of the results you’ve obtained.
Also, remember that the rules of FMEA are actually somewhat flexible, and you can twist them around your current project to some extent. The important thing is to settle on a common set of rules from the very beginning, before even starting the FMEA implementation in the first place. Otherwise you might run into some conflicts with the way your data is analyzed later on, and you may even invalidate the whole FMEA run if the problem is bad enough.
Download a free FMEA template at: https://opexlearning.com/resources/fmea-template-fmea-example/9065/
Long-term benefits
Applying FMEA correctly and consistently can lead to some great improvements in the long run, and it’s one of the best things you can do for your business if you’re having trouble with different types of failures. You can end up working with a system that’s much more consistent and predictable, giving you results that you can actually count on at every step.
On the other hand, you’ll also have a very solid foundation for troubleshooting any issues that come up in the process. This is important by itself, as many organizations tend to have a lot of knowledge about potential issues they can encounter, but very little information on how to actually deal with those issues adequately.
Conclusion
Failure mode and effects analysis can be a great complement to the operation of any organization that has to deal with failures on a regular basis, but it has to be applied correctly in order to get its full benefits. As long as you define a set of ground rules appropriately and work with them all the way, you should be able to process your results correctly and make something sensible out of them.
No responses / comments so far.