The 8 Forms of Deadly Waste in Lean Six Sigma
Lean Six Sigma is one of the most advanced and effective methodologies available for business process improvement and optimization. It is especially adept in battling a wide range of problems and inefficiencies. To help better understand and deal with waste, this approach classifies them into the 8 Forms of Deadly Waste. This classification is important because it makes waste much easier to uncover and then eradicate. It also helps you identify environmental improvement opportunities.
The 8 Forms of Deadly Waste can be easily remembered with the mnemonic DOWNTIME:
- Defects
- Overproduction
- Waiting
- Non-value added processing
- Transportation
- Inventory
- Motion
- Employee skills underutilized
Let’s examine each one individually:
Defects
Whenever a business process ends up with an outcome that was not the desired one, all the effort and resources that had gone into producing it would have been wasted. This is why defects and errors of any sort are always undesirable, and are always a major source of waste. This does not just apply to manufacturing, but to providing services to clients and especially processes internal to the company.
Overproduction
We all know that overdoing anything in our personal life is something to be avoided, but this is a type of waste that often goes completely unnoticed in the business world. Whenever something is produced in a higher amount that was necessary, it’s a type of waste, Worst of all, it also multiplies all the other wastes through the rest of the processes. Overproduction often stems from the inability to estimate and forecast business correctly, and from fear of being late with deliveries. However, it is an expensive and risky way to protect against late deliveries to the customer.
Waiting
Any idle time that is part of a business process is actually time wasted. If a step in the process has to be delayed while waiting for raw materials, parts, equipment, instructions or information, it is always going to lead to waste, since the organization’s potential productivity is going to be squandered. That time cannot easily be made up except through overtime and delayed shipments. Every time work stops, it’s a waste, and an opportunity to improve.
Non-value added processing
When trying to standardize an activity, many businesses experience the pitfall of adding steps to a process that are not actually adding value. This means that all the resources and time that go into those steps are wasted, and could have been used to produce value instead. Examples of this type of waste might vary from having the same thing reported twice in the same spreadsheet or report, to having an unneeded layer of packaging to a product that does not add any value to the customer or protect the product from damage while being transported.
Transportation
Most businesses processes tend to include transporting materials, people, products, equipment, tools or even information and very often at least some of that turns out to be unneeded. This is really an activity that doesn’t add any real value to a process and is a common point of possible failure. This means that excess transportation leads to a lot of waste and could have adverse effects on the reliability of the outcome on top of that.
Inventory
Inventory waste is especially dangerous despite the fact that it sounds quite benign at first glance. Whenever there is an excess supply of materials, information or products, it is often a sign of deeper inefficiency or inadequacy of the current state of the process involved. Everything that stays in inventory instead of being utilized has required an input of resources to get to where it is and all of those resources have been used quite inefficiently. Additionally, while something is in inventory it is always subject to deterioration, so its value will always decrease while the cost of having it around will steadily become higher.
Motion
Motion requires both time and energy and no matter if the motion is physical or virtual, an excess of it is bound to slow a process down and create significant waste. This is a very intuitive concept, it’s just essential that one applies it to everything from physical movement of people and machines to unnecessary movement of files on virtual systems.
Employee skills underutilized
The workforce available to a business is one of its most important assets and resources, and forms a significant part of the cost of providing the customer with the product or service sold. As with any other resource, not using it to its full potential is a waste. But humans are creative and are natural problem-solvers, which means that allowing them to apply their abilities, skills and experience would always lead to unpredictable positive benefits to the business.
Connection to the Environment
In addition, these 8 forms of waste have an environmental impact as well.
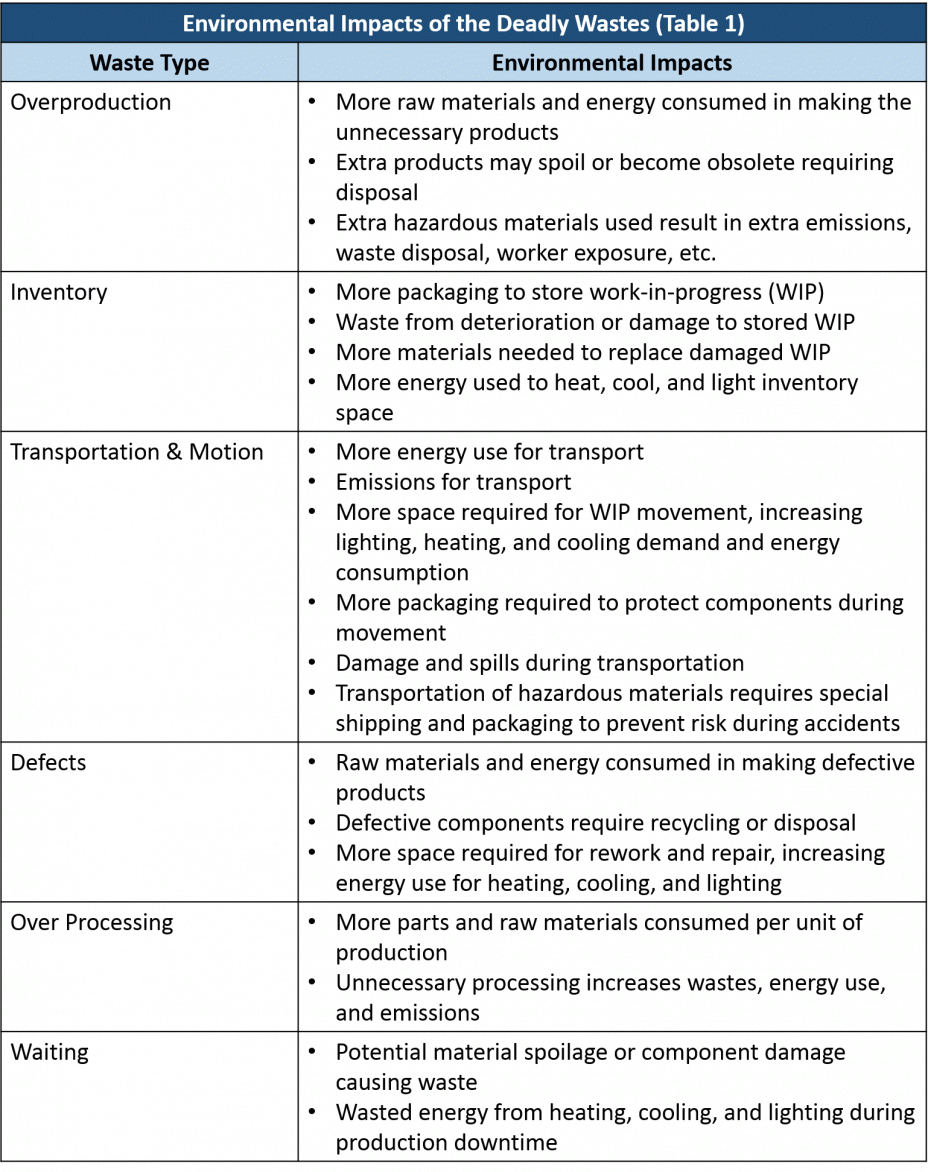
Defects and overproduction can lead to items needing to be disposed of. Inventory requires extra floor space, lighting, heating and cooling. Waiting pushes out the work, requiring overtime and more energy to keep the lights on. Transportation requires fuel and extra packaging. If you’d like to learn more about the environmental impact of these wastes, check out the EPA Lean and the Environment toolkit >>>
Next time you are evaluating a process, look for DOWNTIME opportunities to reduce time and reduce your environmental impact.
To learn more about Lean, download the Toyota training slides >>>
No responses / comments so far.